Where to I place my axle stands while working on the car? Hi! First I just have to congratulate you to a awesome page covering the A-Class! I'm really impressed.
I'm a bit of a petrol head myself but mostly doing BMW's
However I'm about to do a minor job on a A140, so I found your page. But there is one thing I (and I assume
some A-Class owners as well) haven't been able to find any info about - where do you place your jack-stands?
I'm not really used to have a jack-points poking out thread plastic sheets - but I must say it was really
easy and nice to use those. But the question is - where do I place the jack-stands?
I could not really find an answer on that question. I'm about to do a smaller front brake job and would like
to remove one front wheel at a time (I will never crawl under the car supported only by a hydraulic floor jack).
Have you seen any info in the A-Class community regarding where to place jack-stands?
|
A good question but a not so straight forward answer. Unless you have had the plastic under floor pans lowered on your car you will be sceptical about the jacking points which as far as Mercedes-Benz is concerned are there for supporting the vehicle while you remove and then re-fit a spare wheel. They do not envisage you needing to jack the car for any other reason, as they will be doing all the work and maintenance on the car !
Wrong! Many owners simply cannot afford garage prices and more to the point, Mercedes-Benz workshop prices to service their beloved car. and in some case owners like myself prefer to do their own maintenance albeit is not possible to do some of the larger jobs due to the engine having to be dropped.
So where do we place jacks and axle stands.
Well the 4 jacking points are secure being mounted onto the under floor of the vehicle In addition you can jack with care under the wishbones (front Suspension) or on the cross member set to the rear of the front spoiler, which is part of the engine sub frame in addition you have the rear sub-frame, all sound jacking points with care. However when placing jacks or axle stands make sure you do not damage flexible as well as metal brake hoses and pipes etc.
Do not jack or support the car on any part of the car's bodywork or structure unless you have first ascertained the structure of the cars underside, where possible use blocks which spread the load rather than using a single point of support such as the head of an axle stand.
Never rely on jacks alone, for further details
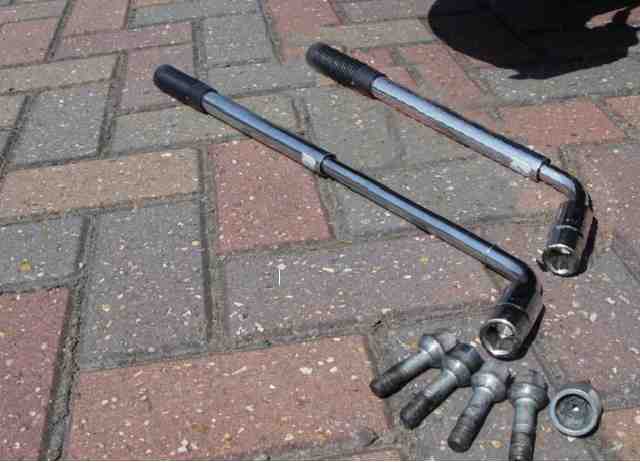
Note the two positions of the brace, It is good practice where possible to have a tray or box to put nuts bolts and components in thereby keeping them dirt free. .
Having correctly sited the jack but before taking any real weight off the wheels it will be necessary to slacken the wheel bolts, including the locked bolt. This is easiest done with an extending wheel brace which these days can be purchased quite cheaply. Having slackened the bolts we now have to jack up the car and will need the jack handle. When using the jack handle, place it on the jack fitting it over the hexagonal nut, movement clockwise raises the jack, anti clockwise lowers the jack. To achieve the direction you require, reverse the handle on the nut as the ratchet on the handle only works one way. Top Tip to save your knuckles having placed the got the jack handle in position place the pad of your thumb on your now spare hand onto the end of the hexagonal drive ,this will stop it keep slipping off, Ouch! 1 The wedge in this photo would be of more effective if it was placed the other side of the car, unless of course you have two! When we come to replacing the bolts following a service/inspection, a small amount of grease applied the last few treads of each bolt will ensure the they run up easily, place them in the socket and start them off Rotating the socket by hand to engage the first bolt you may have to rotate the wheel to align to holes with the hub. This way you are not so likely to cross thread them (Damage the thread). Having got them all started use the brace with the extending bar closed (shortest mode) this way you are less likely to over tighten them, as soon as possible check them with a torque wrench. (110Nm)
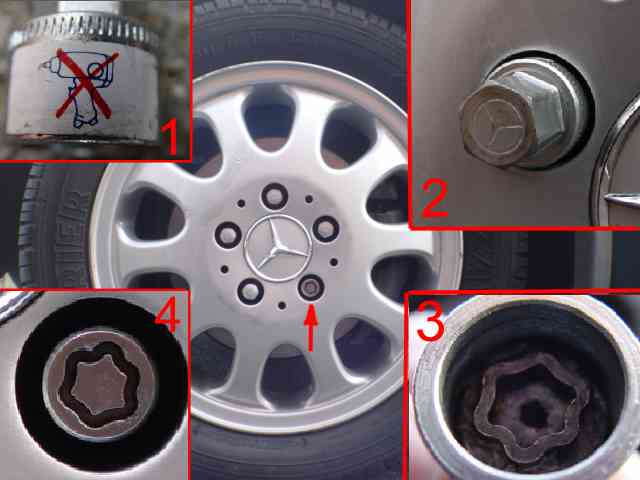
1 key 2 Standard Hexagonal Head 3 Inside of key Showing Male Keyway. 4 Female keyway in Wheel bolt. I have it on good authority that in tests MB's locking wheel bolts came out well in tests, so your wheels are safe. But remember you cannot get them off without the key, keep it very safe. Good wheels cost Good money, it is of course essential that you carry the lock-key in the car, although not necessarily any ware obvious, remember to make it available on any occasion where there my be a need to remove a wheel.
Again its worth making the Garage or Tyre Fitting Company aware that you would appreciate them observing the No Power/Pneumatic Tools rule when using your key or severe damage could be caused. I understand from MB that they have keys to fit wheel bolts provided by them, however if the need arose for them to assist you it is likely to cost you a fortune. If in the circumstances they would consider your request at all.
Replacement locking wheel bolt keys are available from MB, however you will need to provide a wheel bolt or existing key to determine the code. MB Part No MB 6 40 82XX the last two digits denote the code for your specific wheel nuts.
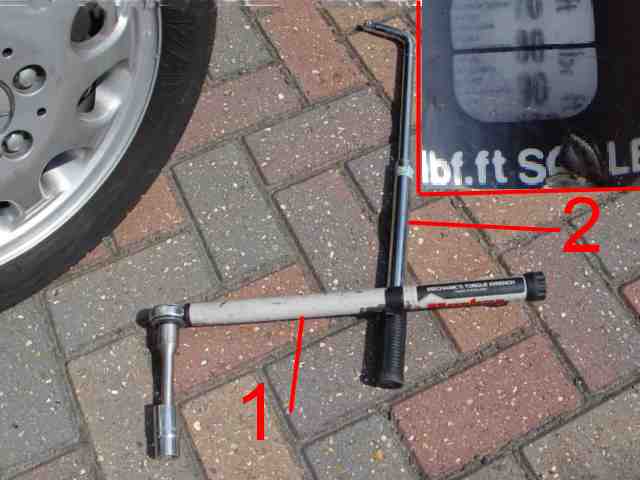
Finish off the tensioning of the wheel bolts with the torque wrench , tighten to 110 Nm, or 80ft.lbs. When tightening all bolts do not apply shock, tighten by applying gradual pressure. to alternate bolts until all five reach to correct tightness. Pneumatic/Air powered tools, should not be used on the key of the locking wheel bolt kit.
Special Notice If you are temped to follow some of my methods then please only do so if you feel fully competent, remember cars a lethal weapons in the wrong hands and also if poorly maintained. Do not short cut on materials, or spares you will save pounds doing little jobs and checking things like exhaust hangers, checking brakes and carrying out inspections prior to MOT's but the initial investment will only be recouped as long as you are not Accident Prone? If that is the case then leave well alone. Better be safe than sorry.
|